The Science Behind Porosity: A Comprehensive Overview for Welders and Fabricators
Recognizing the intricate mechanisms behind porosity in welding is crucial for welders and fabricators striving for impeccable workmanship. As metalworkers explore the depths of this phenomenon, they discover a globe controlled by numerous variables that affect the development of these small voids within welds. From the structure of the base products to the ins and outs of the welding procedure itself, a plethora of variables conspire to either exacerbate or reduce the presence of porosity. In this comprehensive overview, we will certainly decipher the science behind porosity, exploring its effects on weld top quality and introduction advanced strategies for its control. Join us on this trip with the microcosm of welding blemishes, where accuracy meets understanding in the quest of remarkable welds.
Recognizing Porosity in Welding
FIRST SENTENCE:
Examination of porosity in welding discloses vital insights into the honesty and quality of the weld joint. Porosity, defined by the presence of tooth cavities or gaps within the weld metal, is a typical worry in welding procedures. These voids, if not appropriately addressed, can jeopardize the architectural stability and mechanical residential properties of the weld, leading to potential failures in the completed item.
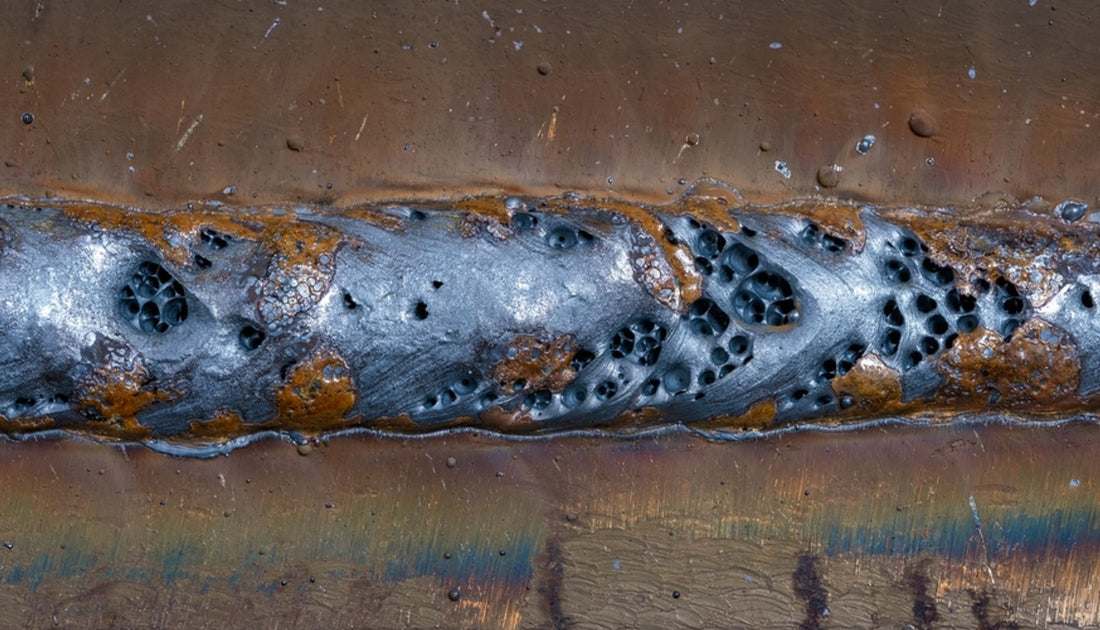
To identify and evaluate porosity, non-destructive screening approaches such as ultrasonic screening or X-ray inspection are often employed. These strategies permit the identification of internal issues without endangering the stability of the weld. By examining the size, form, and circulation of porosity within a weld, welders can make informed choices to boost their welding procedures and achieve sounder weld joints.
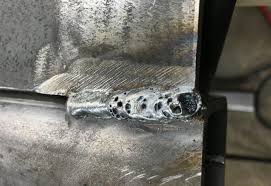
Aspects Influencing Porosity Formation
The occurrence of porosity in welding is influenced by a myriad of elements, ranging from gas protecting efficiency to the complexities of welding parameter setups. One crucial variable adding to porosity formation is inadequate gas securing. When the shielding gas, typically argon or carbon dioxide, is not efficiently covering the weld swimming pool, climatic gases like oxygen and nitrogen can contaminate the liquified steel, causing porosity. Additionally, the sanitation of the base materials plays a substantial role. Impurities such as rust, oil, or wetness can evaporate during welding, developing gas pockets within the weld. Welding specifications, including voltage, existing, travel rate, and electrode kind, additionally effect porosity development. Using incorrect setups can produce too much spatter or heat input, which consequently can cause porosity. The welding strategy employed, such as gas metal arc welding (GMAW) or shielded steel arc welding (SMAW), can influence porosity formation due to variations in heat distribution and gas protection. Understanding and regulating these factors are crucial for decreasing porosity in welding procedures.
Results of Porosity on Weld Top Quality
The visibility of porosity additionally damages the weld's resistance to deterioration, as the trapped air or gases within the gaps can react with the surrounding atmosphere, leading to deterioration over time. Additionally, porosity can impede the weld's ability to hold up against pressure or influence, more endangering the total quality and reliability of the welded structure. In essential applications such as aerospace, automotive, or architectural building and constructions, where safety and longevity are vital, the damaging results of porosity on weld top quality can have extreme effects, stressing the importance of reducing porosity with appropriate welding methods and procedures.
Methods to Reduce Porosity
To improve the top quality of welded joints and make certain architectural integrity, welders and makers employ specific strategies targeted at decreasing the development of gaps and dental caries within the material during the welding process. One reliable technique to minimize porosity is to ensure appropriate product preparation. This consists of thorough cleansing of the base metal to remove any kind of contaminants such as oil, oil, or wetness that might contribute to porosity formation. Additionally, using the proper welding specifications, such as the right voltage, current, and travel rate, is vital in stopping porosity. Maintaining a regular arc size and angle during welding likewise helps in reducing the chance of porosity.

Furthermore, picking the appropriate shielding gas and preserving proper gas flow rates are vital in reducing porosity. Making use of the suitable welding method, such as back-stepping or using a weaving motion, can likewise aid disperse heat uniformly and lower the chances of porosity formation. Making sure correct air flow in the welding environment to remove any prospective sources of contamination is essential for achieving porosity-free welds. By implementing these techniques, welders can efficiently reduce porosity and create top notch welded joints.

Advanced Solutions for Porosity Control
Implementing advanced innovations and innovative approaches my site plays an essential role in attaining remarkable control over porosity in welding processes. One sophisticated solution is using sophisticated gas mixtures. Securing gases like helium or a blend of argon and hydrogen can help reduce porosity by giving much better arc security and enhanced gas insurance coverage. Furthermore, employing sophisticated welding methods such as pulsed this link MIG welding or changed environment welding can additionally assist minimize porosity problems.
An additional advanced service includes the use of innovative welding tools. Making use of tools with built-in features like waveform control and sophisticated power resources can boost weld top quality and lower porosity risks. Additionally, the application of automated welding systems with precise control over specifications can substantially lessen porosity issues.
Additionally, integrating advanced monitoring and inspection technologies such as real-time X-ray imaging or automated ultrasonic testing article can aid in spotting porosity early in the welding process, enabling prompt restorative actions. Overall, incorporating these sophisticated services can significantly improve porosity control and boost the general quality of bonded elements.
Conclusion
Finally, recognizing the science behind porosity in welding is important for welders and makers to create top notch welds. By recognizing the aspects influencing porosity development and executing techniques to lessen it, welders can enhance the total weld high quality. Advanced solutions for porosity control can additionally enhance the welding procedure and make sure a strong and trusted weld. It is very important for welders to constantly enlighten themselves on porosity and execute ideal practices to attain optimal outcomes.